There has been a rise in demand for power semiconductor modules due to a boost in the electric vehicles’ market, writes Hitesh Bhardwaj, General Manager, Mitsubishi Electric India
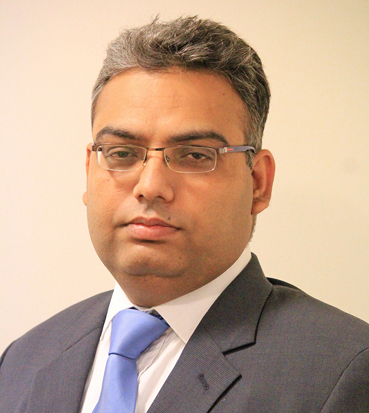
The automotive industry has seen major advancements with the world of smart technology shifting towards battery-operated vehicles. Producing over 60 million cars and trucks annually around the world, the industry is currently undergoing a paradigm shift, attempting to make a quick transition to alternative energy sources. India is also in the same boat, attempting to invest in the shift to electric mobility. After considering various factors such as the hassle of oil imports, global climate change issues, major scarcity of natural resources, attainment of sustainability, rising pollution, and so on, this idea has gained traction.
The Government of India has proposed several changes to the Central Motor Vehicles Rules, 1989 to encourage electric mobility in India. It recently proposed exemption to battery-operated vehicles (BOVs) from paying fees for the issuance or renewal of a Registration Certificate (RC) as well as the assignment of a new registration mark. It has also increased the subsidy for electric two-wheelers under the Faster Adoption and Manufacturing of Electric Vehicles–Phase II (Fame II) scheme. The government has also increased the demand incentive for electric two-wheelers by 50% to 15,000 per kWh, up from the previous uniform subsidy of 10,000 per KWh for all-electric vehicles (EVs) and hybrids, except for the buses.
Charging Stations: A Priority Issue
There is no denying that the number of battery electric vehicles (BEVs) on the road has risen dramatically in the last five years. India aspires to become a major global vehicle market with several automakers and start-ups working on relevant products and technology-enabled gears. In India, the growth of e-mobility requires mandatory installation of EV charging stations. The charging infrastructure is a critical factor to determine the country’s EV adoption possibilities. Since EVs run on batteries, the massive operation of the vehicle leads to the requirement of frequent recharging of the battery technology, which also depends on the size and capacity of the battery.
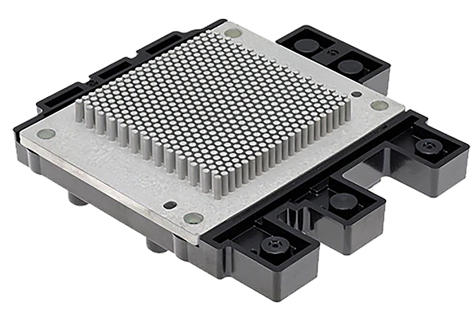
As a result, charging stations are critical for the long-term operation of electric vehicles. The charging requirements are determined by the type of vehicle as well as the utility purpose. According to the NITI Aayog report, there is a possibility that India can have a high level of electric vehicle penetration by 2030. The Indian government has ambitious plans to switch to electric vehicles (EVs) on a large scale by 2030. While the transformational push for electric vehicles is a great step forward for India and the world, it brings with it a slew of opportunities as well as challenges. Mitsubishi Electric India has already taken a step towards making the transition to electric vehicles a reality on a large scale.
Mitsubishi Electric Power Semiconductors
The J1 series power semiconductor with a direct water-cooling (pin-fin) structure has been in operations for a few years by the company, mainly for motor drive applications in electric and hybrid vehicles. By 2030, the Government of India aims to electrify 70% of all commercial vehicles, 30% of private cars, 40% of buses and 80% of two-wheelers and three-wheelers. Not only the Indian government but also industry giants have expressed optimism about the growth of electric vehicles and charging stations in India. India is gradually catching up with the rest of the EV charging ecosystem, based on recent developments. Automotive components must meet stringent safety standards, a fact which creates a high demand for power semiconductor modules by power semiconductor manufacturers that provides more reliability than industrial equipment modules.
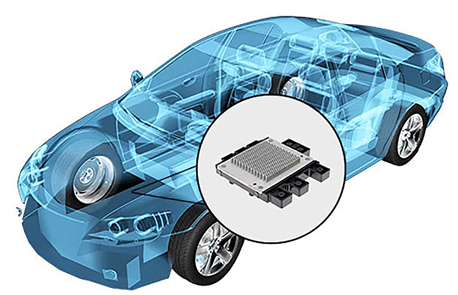
In 1997, Mitsubishi Electric became the first company to mass-produce power semiconductor modules for hybrid vehicles. The company’s new power semiconductor module is expected to contribute to further compactness, weight reduction and reduced power consumption in inverters for electric and hybrid vehicles. This helps Mitsubishi Electric claim to be one of the best power semiconductor manufacturers. The power semiconductors by Mitsubishi Electric have some cutting-edge features, such as a smaller and lighter inverter due to the extra compact package and high integration. The compact power semiconductor module features a highly integrated seventh generation IGBT with a carrier-stored trench-gate bipolar transistor (CSTBTTM) structure and seventh generation diodes.
The direct cooling pin-fin structure achieves 30% lower thermal resistance and 40% smaller footprint. Another noteworthy feature is that each IGBT chip in the power semiconductor devices is equipped with a current sensor for short-circuit protection as well as on-chip temperature sensing for over-temperature protection. This allows the chip temperature to be directly monitored. The power semiconductor device in the J1 series no longer uses heat sink grease as required by the previous structures; instead, the power semiconductor device is equipped with a cooling fin integrated with the module to allow direct cooling and in turn, improve the cooling performance.
Also, by optimising the shape and layout of the fin in the power semiconductor device, and eliminating the solder layer beneath the isolation layer, the thermal resistance between the chip and the cooling water is reduced by more than 30% compared to the level of a conventional product, which consists of three J series transfer-moulded power modules (T-PMs) mounted on the copper cooling fin with the heat sink grease between them. The cooling fin material for the power semiconductor devices in the J1 series is aluminium, which provides high corrosion resistance against water cooling and significantly reduces assembly weight when compared to the conventional product.
The new module is also automotive-grade high quality and adopts Mitsubishi Electric’s original direct lead bonding (DLB) structure that leads to 30 times’ longer power cycle and temperature cycle life than those of typical industrial power semiconductor modules. Not to mention, the EV ecosystem is reliant on government policy intervention, private sector participation and, of course, technological advancements in the EV charging space. As a result, it is important to keep an eye on these developments as well. EV charging stations are the backbone of the e-mobility industry, and properly constructing them will undoubtedly increase EV adoption in India. A high jump to EV usage can contribute to a sustainable and developed nation by helping in optimised usage of fuels and other natural resources which needs to be conserved for a better future.