By Martin Kunz, President and CEO, Concentric AB
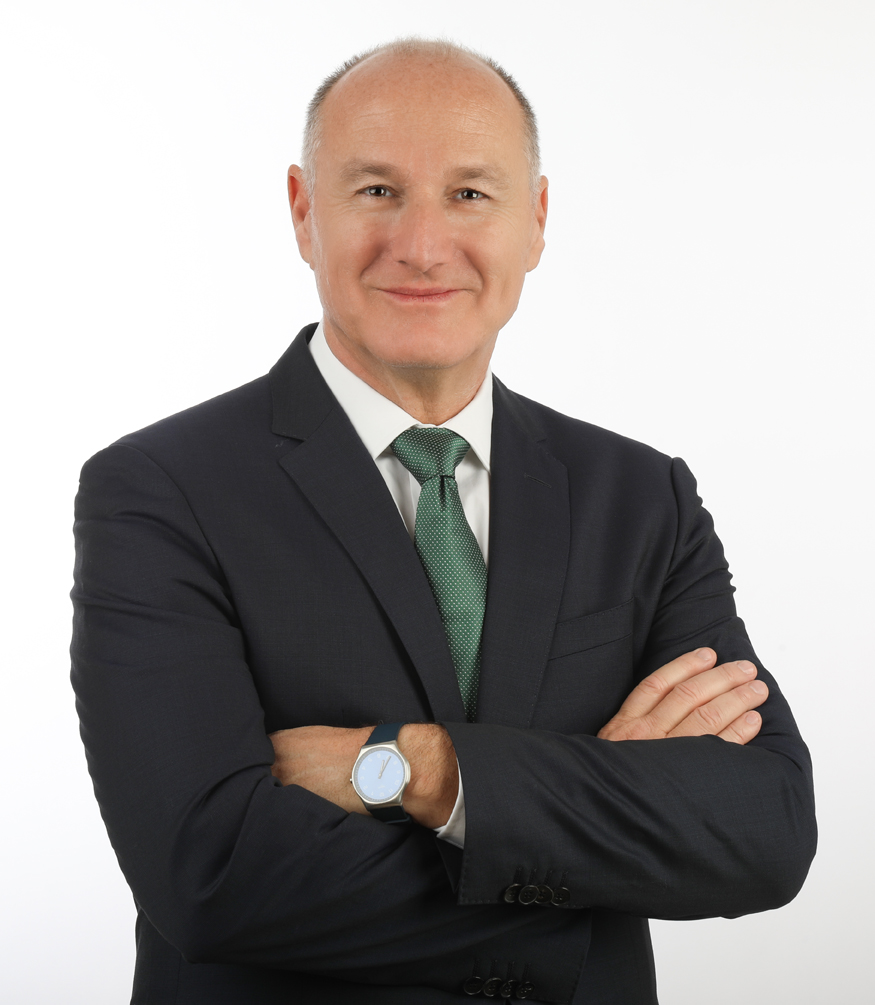
Manufacturers of construction equipment are facing a complex challenge: they need to curb emissions as well as reduce dependency on diesel fuel, and they need to do it as quickly as possible. Is the electrification of construction vehicles a viable step in the right direction, and if so, how can the process be expedited?
Electrifying construction vehicles: a perspective
According to independent market research company IDTechEx in its report entitled ‘Electric Vehicles in Construction 2022-2042’, the decarbonisation of the construction industry will play a critical role globally for countries to meet their 2015 Paris Agreement commitments, and the electrification of construction vehicles, including excavators, loaders, cranes, and telehandlers for example, will be key in helping construction organisations to achieve their environmental targets.
“Construction machines are responsible for around 400 Mt of CO2 emissions annually, which is around 1.1 percent of global CO2 emissions,” details the report, further stating that, while the off-road electric construction vehicle market is at a much earlier stage of development than the on-road electric vehicle sector, there is increasing effort within the space to deliver zero emission solutions, with a growing number of prototypes.
What we’re seeing currently is that the electrification of construction vehicles is being led by smaller, more compact machines, for example mini-excavators, small wheel loaders and dump trucks. This is largely because these machines are deployed in urban environments, and cities are increasingly looking to lower exhaust emissions and noise, with electric construction equipment having the added benefit of low-noise zone compliance. This in turn provides a safer, more comfortable working environment for employees, as noise and vibration are reduced in electric assets, thus reducing the chance of hearing loss and fatigue.
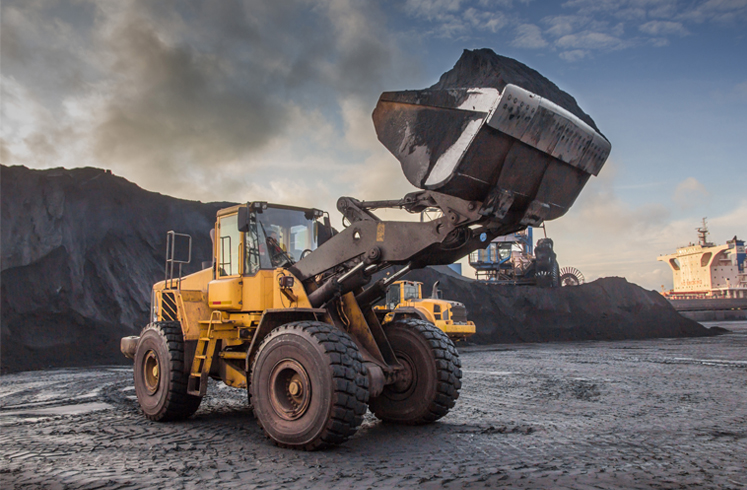
In addition, because they are being used in smaller projects, the daily duty cycle – and accordingly power demand – of smaller machinery is lower than for larger machines. Thus, a standard eight-hour workday for the smaller pieces of equipment can be met with a practical size of Li-ion battery (less than 50kWh) and electric motor (less than 20kW).
And while this in itself is good news for the sector, it is even more encouraging that heavier construction machines, which contribute significantly more to the sector’s CO2 emissions, are also starting to embrace lower-emission solutions. The question is: Why?
According to McKinsey, Total Cost of Ownership (TCO) could be a major driver in the electrified heavy machinery market. The global management consulting firm has predicted that by 2023, the TCO of heavy electrified machinery could be up to 21 percent lower than that of similar internal combustion engine (ICE) equipment. This is driven by a 40 to 60 percent lower operating cost reduction, thanks to reduced fuel consumption, and a simpler drive-train with fewer moving parts, requiring less maintenance.
The role of electric power sources
As the electrification of the construction market gathers pace, with major manufacturers like Volvo, Wacker Neuson, Caterpillar, JCB and Bobcat introducing electric alternatives to traditionally diesel-powered construction equipment, organisations like Concentric – which has a long history of supporting OEM customers within the industry through technologically advanced, robust and reliable solutions – will play an increasingly significant role.
As pressure mounts for construction firms to adopt more efficient solutions, so too will the requirement to include electric pump (e-pump) technology in hybrid or fully electric machines. In line with this, the company has developed a range of electric pump solutions to assist with building reliability, fuel economy, control and emission reduction improvements.
Developed for the cooling of hybrid and electric vehicle batteries and power electronics, the e-pump has been designed to meet the challenges of heavy-duty commercial vehicles, including installation vibrations, and dust and water resistance.
Concentric is currently developing products that enable the use of high voltage supply, including both pumps and fans, providing durable, powerful yet efficient and space-saving solutions. At this time, we are the only firm in the industry to offer high voltage fans.
With its global footprint and extensive industry experience in conventional pumps, Concentric is currently in conversation with several leading blue-chip OEMs within the construction industry to support their electrification journeys, deploying a number of pilot projects.
By way of example, Concentric recently received a new development contract to supply high voltage electric coolant pumps for a battery electric mining machine. The customer, a global construction OEM, will use the e-pumps for cooling the batteries and power electronics on a large, fully electric mining machine.
Battery electric powertrains will be one of the key technology enablers for zero emissions from off-highway machines, and this new agreement is another innovation milestone in the development of Concentric’s e-pumps.
As a leader and innovator in flow control and fluid power, Concentric is working towards a sustainable and carbon neutral future, continuing to invest in technology that can deliver on the rapidly evolving needs of the market, and actively supporting organisations in their electrification process.