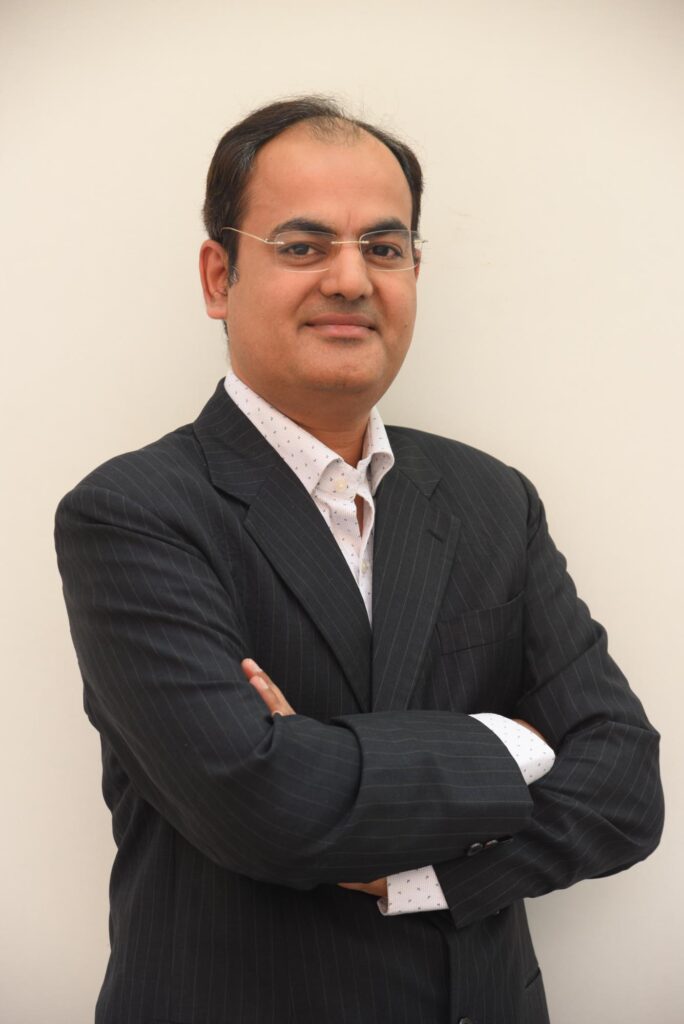
Rajesh Rajgor explores how Vedanta Aluminium, under Alok Ranjan, Chief Marketing Officer, is advancing lightweighting and sustainability in the automotive sector. With a diverse portfolio of foundry alloys, billets for EVs, and the low-carbon Restora range, the company supports automakers in enhancing efficiency and safety. Its AI-powered Vedanta Metal Bazaar and Jharsuguda Aluminium Park streamline procurement and supply, reducing costs. Focused on R&D and OEM collaboration, Vedanta Aluminium is driving the industry’s transition to EVs and next-gen mobility solutions.
With increasing aluminium adoption in EVs, ICE, CNG, and LNG vehicles, how does Vedanta Aluminium support automakers in lightweighting solutions? What innovations are in the pipeline to enhance vehicle efficiency, safety, and performance across all fuel types?
Aluminium’s exceptional strength-to-weight ratio makes it an ideal choice for lightweighting vehicles. Every kilogram of aluminium used reduces the overall vehicle weight by the same amount, an especially important factor for electric vehicles (EVs) where reducing 100 kg in terms of weight can increase the vehicle’s driving range by 10-15%. Hence, hybrid and fully electric vehicles today feature up to 27% more aluminium usage than internal combustion engine vehicles.
Vedanta Aluminium is helping automakers achieve efficiency, quality, safety, and sustainability in their products. We offer several advanced products, such as primary foundry alloy for wheels, engine blocks, and cylinder-head applications, as well as billets for use in battery casings, HVAC systems, and EV frames. The billet offerings vary according to the needs of our customers, ranging from higher extrudability to higher strength.
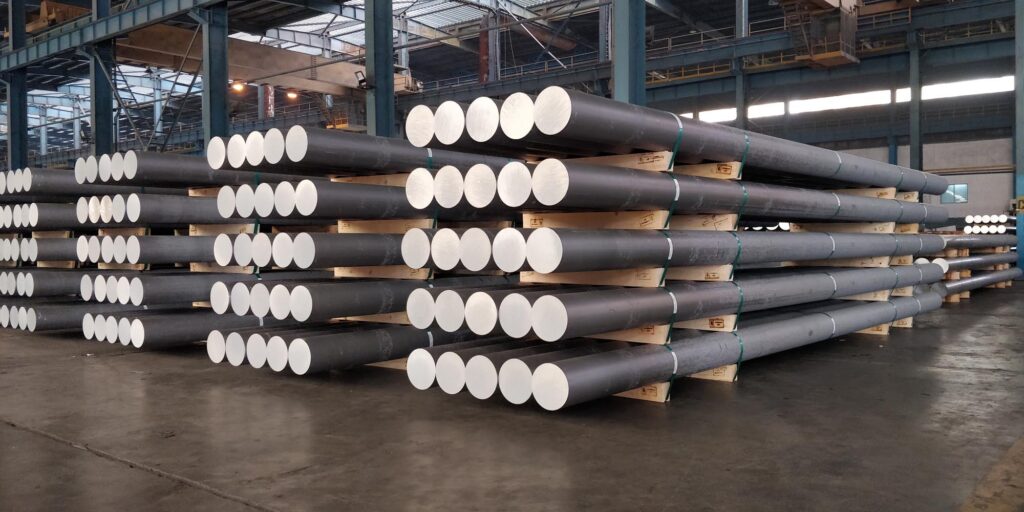
Moreover, we are noticing a significant uptick in the demand for green aluminium, a segment that we cater to through ‘Restora’, India’s first low-carbon aluminium range that includes aluminium manufactured using renewable energy and recovered aluminium dross. So with increased performance, we are also able to offer a greener alternative to automotive manufacturers, in turn enhancing their ability to develop world-class products.
With the introduction of Restora, India’s first low-carbon aluminium, how is Vedanta Aluminium helping automakers meet sustainability goals while ensuring high performance across EVs and conventional vehicles?
With a greenhouse gas emission intensity within 4 tonnes of CO2 equivalent per tonne of aluminium produced, our Restora range caters to customers looking to actively decarbonize their operations and utilize sustainably produced materials in their value chains. The product line also includes Restora Ultra, made from recovered dross and boasting a near-zero carbon footprint. By utilizing renewable sources in its manufacturing process, we ensure that our products not only help reduce emissions but also support the circular economy, making them ideal for both electric vehicles (EVs) and conventional vehicles.
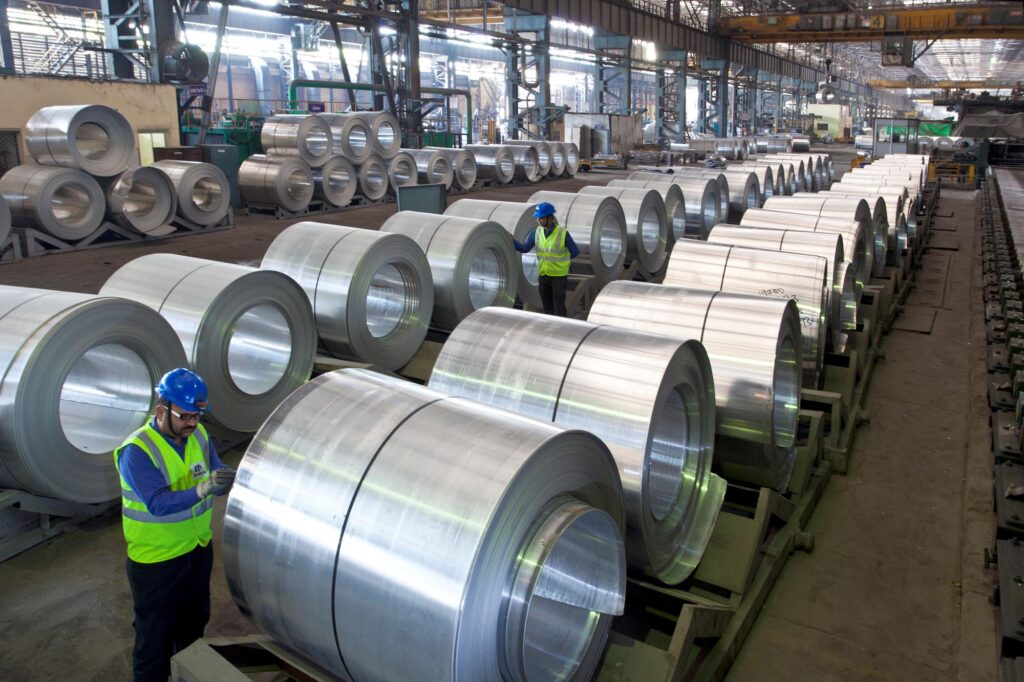
The versatility of Restora allows us to customize it into various forms, such as billets and ingots, to cater to diverse automotive applications. By positioning ourselves as harbingers in low-carbon solutions, we are accelerating the energy transition and enabling greener vehicles to hit the roads, contributing to a more sustainable future for the automotive sector.
The Aluminium Park in Jharsuguda and the AI-powered Vedanta Metal Bazaar offer streamlined access to materials. How do these initiatives support manufacturers of ICE, CNG, LNG, and EV vehicles in optimizing production and reducing costs?
Vedanta’s Metal Bazaar is a revolutionary platform, an extensive e-superstore that offers over 750 aluminium products for customers across diverse sectors. Powered by AI technology, it is designed to simplify the metal buying experience. This digital solution allows manufacturers to efficiently source materials tailored to their specific needs, optimizing supply chains and supporting operational excellence. In addition, there are no limits on quantity of metal purchased, making it a boon for MSMEs engaged in manufacturing auto components.
Further enhancing the value proposition is Vedanta’s Aluminium Park in Jharsuguda, strategically located near our mega aluminium smelter, one of the world’s largest. Spanning 253 acres, the park offers downstream manufacturers priority access to high-quality molten aluminium, significantly reducing the time and costs tied to transportation and re-melting. By minimizing logistical challenges, manufacturers can streamline their operations, boosting productivity, cutting costs, and improving market competitiveness.
With IATF 16949:2016 certification and a focus on crash-resistant billets, how does Vedanta Aluminium ensure its products meet evolving safety, durability, and global performance standards? Are there any new material innovations for structural, thermal, or safety applications in different vehicle types?
At Vedanta Aluminium, we are committed to maintaining the highest quality standards, particularly in the automotive sector, where safety, durability, and performance are paramount. We have secured IATF 16949:2016 certification for our automotive offerings, reflecting our dedication in adhering to stringent quality management systems and international standards.
Our crash-resistant billets are a key outcome of this approach. Specifically designed to absorb energy and deform in a controlled way during impacts, these billets enhance vehicle safety significantly. The advanced 6XXX aeries alloys are perfect for critical applications such as crash boxes and bumpers, offering manufacturers access to materials that ensure compliance with stringent safety requirements in vehicle design.
We also offer specialized primary foundry alloy products for use in high cubic capacity bikes, specifically to manufacture crucial components such as casting rear grips, handle grips, brake levers and others. Further, Vedanta Foundry Alloy (VFA) is used by die casters in various automobile components such as crankcase, clutch housing, engine covers and sensor brackets.
How is Vedanta Aluminium engaging with automotive OEMs and component suppliers across all fuel types to drive material adoption, reduce emissions, and improve vehicle efficiency? What key trends and innovations can we expect in 2025 and beyond?
We leverage our extensive engineering expertise, focused R&D efforts, and dedicated innovation cells to ensure a top-notch experience. Our Customer Technical Services (CTS) team works directly with our customers to design and develop products that cater to their unique needs and requirements. Boosting transparency in manufacturing, we organise regular site visits for both existing and potential customers to ensure that they witness first-hand the technology and processes that go into producing our world-class aluminium.
As we progress further into 2025, we anticipate that the demand for aluminium within the automotive sector will grow exponentially, boosted by the expanding EV market, increased investment in an extensive and robust EV charging infrastructure, and advancements in battery technology.