Interplex, a leading provider of customized interconnect, high-precision and mechanical products solutions, showcased its specialized portfolio of next-generation green energy solutions at Battery Show Europe, held in Stuttgart, Germany from 28-30 June 2022.

As the electric vehicle (EV) and overall e-mobility markets shift into higher growth rates, battery technologies face key assembly challenges, including the need for design flexibility to handle a range of different individual cell types while keeping costs and increasing production volumes. As a global solutions provider, Interplex’s design expertise and vertically integrated in-house production help businesses accelerate their battery interconnect system’s time-to-market.
Batteries for e-Mobility applications generally consist of a design hierarchy including key elements such as Individual Cells, Modules and Battery Packs.
- Individual Cells – the smallest, packaged form of battery, which typically is a Lithium-ion unit delivering one to six volts each.
- Modules – typically consisting of several cells connected together in either series or parallel.
- Battery Packs – final deployable battery systems consisting of multiple modules combined in series or parallel to provide the level of output needed for a specific application.
Individual cells can take a range of different shapes, including cylindrical, pouch or prismatic.
Cylindrical cells provide a symmetrical shape that can be efficiently packed together. These have become the most commonly used cell type and provide for high density packing into modules. The cylindrical shape also helps minimize stress and internal pressures.
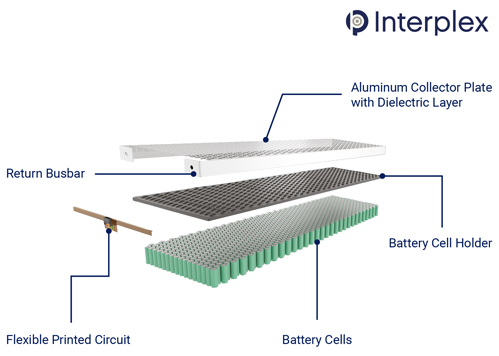
Prismatic cells are typically packaged in a hard casing of welded aluminium or steel. Their low-profile design can improve volume utilization in the module and battery pack. However, prismatic cells can be more expensive to manufacture.
Pouch cells (sometimes called polymer cells) are similar to prismatic cells but, instead of a hard metal casing, they are sealed in a laminated foil pouch. Pouch cells offer a high level of packaging efficiency and can be created in a variety of shapes. However, they may tend to swell and are more vulnerable to penetration than hard casings.
Battery modules typically consist of a large number of individual cells grouped together and connected to current collector plates for gathering the specified power output levels. The number of cells connected in a specific configuration and power output of each cell are the determining factors for delivering the required output for the battery module.
“Interplex can offer flexibility to handle different cell types, robust laser weld or wire bond attachment options for connecting cells to collector plates, customization capabilities to meet any power output and configuration requirements as well as ability to handle design-specific requirements for aluminium, copper, nickel, performance plastics, dielectric layers, etc. in an optimized packaging to accommodate harsh vibration and environmental specifications”, said Randy Tan – Product Portfolio Director, Energy, Interconnect of Interplex.
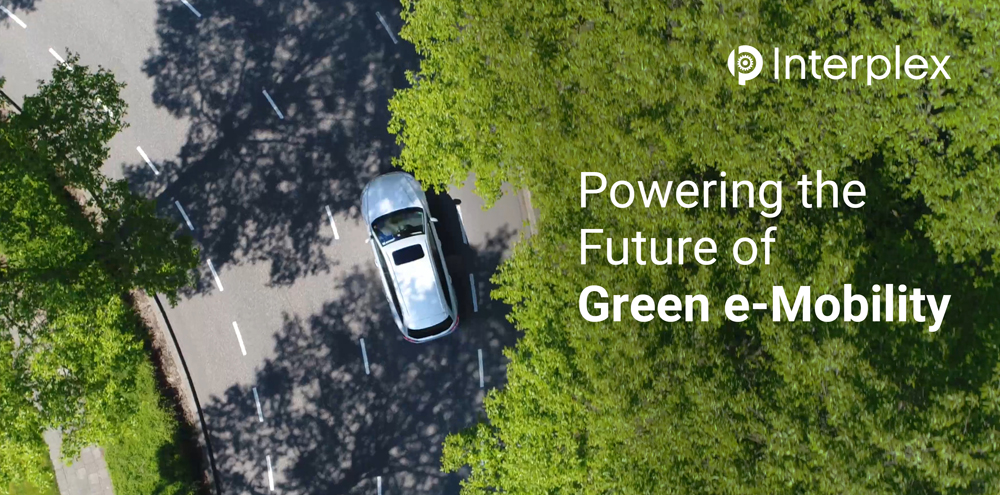
The Cell-PLX™ battery interconnect system from Interplex is specifically designed to provide electric power to the vehicle, enabling battery manufacturers across the entire spectrum of applications to have a single robust, customizable, safe and cost-effective solution that addresses the full range of design requirements.
Cell-PLX™ provides options for high speed, robust laser weld attachment to the cells, thereby enabling efficient production processes, lower manufacturing costs, and high-volume operations. It has been designed to provide full conformance with all applicable standards that are currently used within the automotive industry and also provides the built-in flexibility for adapting to any new EV-related standards as they evolve and are adopted.